During our last offseason, our team acquired two brand new CoreXY 3D printers, manufactured by the Brazilian company GO3Ds.
But first of all, we should introduce some concepts on 3D printing to explain 5800’s need for a 3D printer and what had us picking this type.
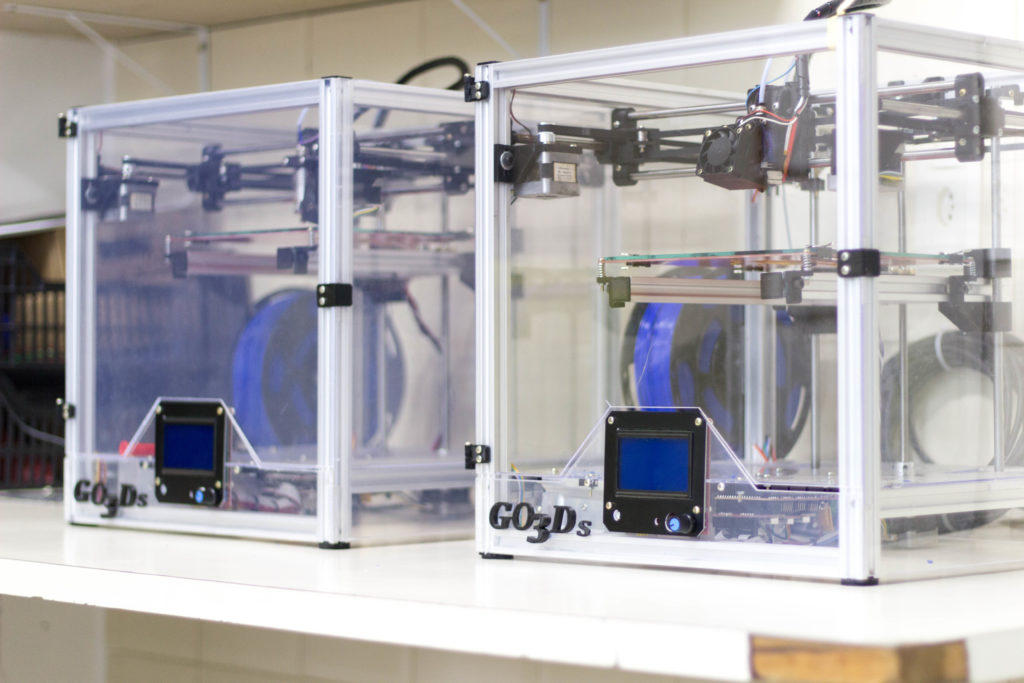
A bit of background on 3D Printers:
Even though it may pass as new technology, 3D printing has been around since the ’80s, which means it’s been a thing for nearly 30 years.
That sure is a long time, right?!
The man considered the creator of 3D printing is a North American engineer by the name of Chuck Hull, who invented and used the stereolithography method to create the first 3D printer.
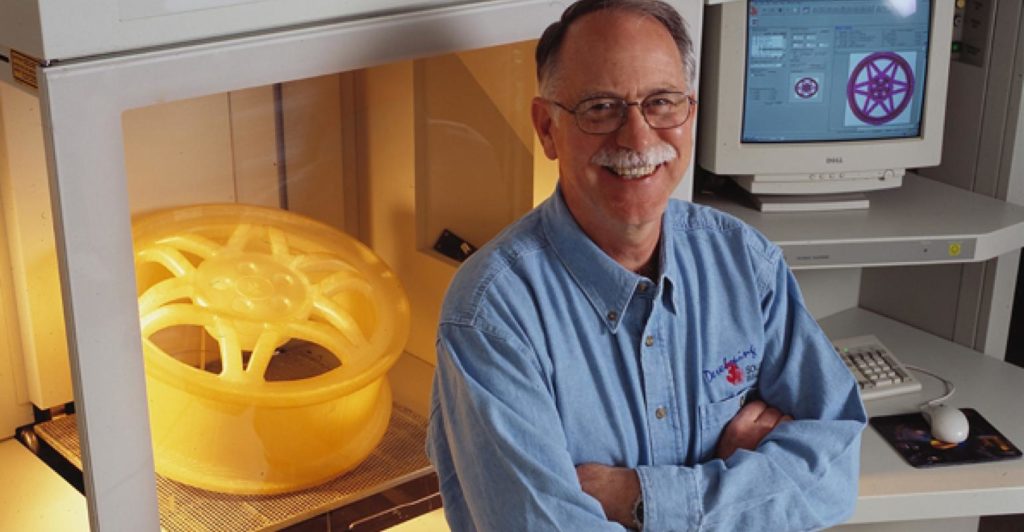
Em 1986 ela foi patenteada e em seguida Hull montou a fábrica 3D Systems que é referência mundial no setor até hoje.
3D printers that use the stereolithography method work by focusing an ultraviolet (UV) laser on to a vat of photopolymer resin.
Usually, the object printed through this method needs a bit of remodeling when it’s finished.
There are new models of 3D printers being created every day. The printers are created for the industrial and professional market, but they can also be purchased to be used at home.
Some of the other methods used for 3D printing:
- Fused deposition modeling (FDM): The most popular method, which builds objects layer by layer from the very bottom up by heating and extruding thermoplastic filament. (This method is one of the methods used by our team)
- Digital Light Processing(DLP): very similar to stereolithography, the method uses digital micromirrors laid out on a semiconductor chip.
É bom lembrar que dependendo do método da impressora escolhida o preço dela pode variar muito, podendo custar R$800,00 ou até R$45.000,00. Vai de acordo com a necessidade de aplicação e a quantidade de detalhes exigidos.
Our method:
Since we use an FDM it’s good to highlight some elements not mentioned previously.
Even though it shows a few limitations, this printer brings advantages such as durability to the printed object, the printer is small and relatively simple to operate and to preserve, and the best part: it has the lowest production cost of all the other technologies.
The file format that the printer uses is usually .STL.
Do you know how a 3D printer works?
The first step to printing a solid object is to model the selected object through a modeling software.
An example of a modeling software is the program SolidWorks, which is a program that is very popular in the robotics community. Our team, FRC5800, uses SolidWorks for our own creations, among other projects.
After modeling the object, the model must be converted into a file, the file format may vary, depending on the programs and printers used to create the piece.
Once the raw material is added, the object is then printed, layer by layer, until the creation is completely finished.
It’s good to mention that there are repositories where we can find already produced 3D models provided by other FRC teams, but it’s not just robot parts that we can find on websites such as THINGIVERSE, Cult3D, Grabcad. With the 3D printers becoming so popular, multiple people have already modeled and printed objects for your home and toys, among other things.
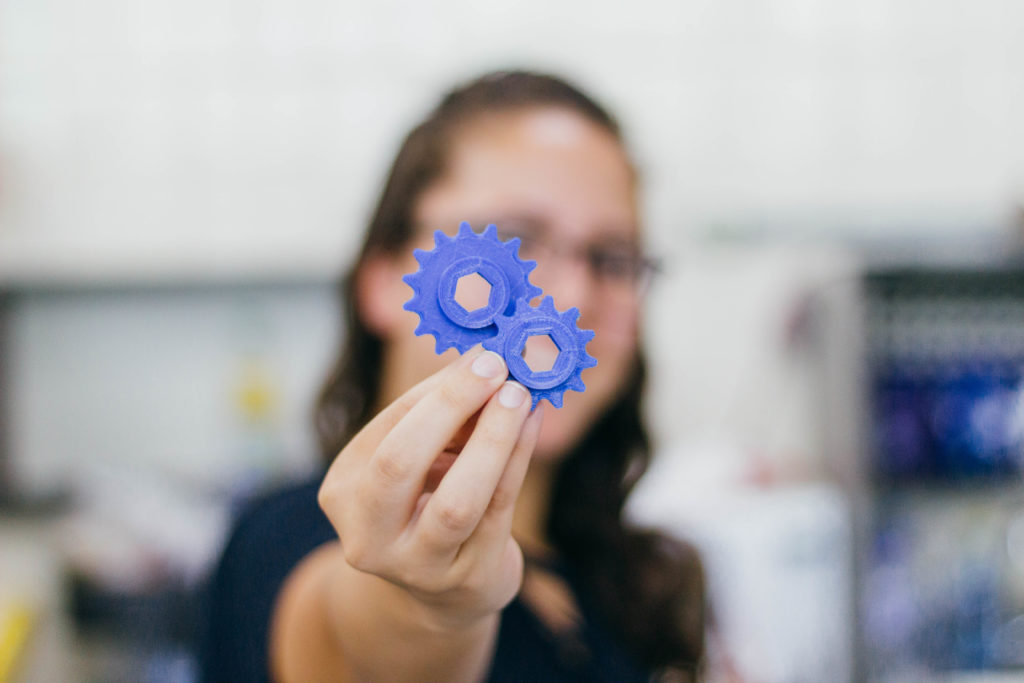
Why does our team, FRC5800, need 3D printing machines?
While building the robot, our team is in constant need of very specific parts and pieces that are, most times, very difficult to find and afford.
Thus, the purchase of the 3D printer is an effective and practical way for our team to get the parts they need to build the robots.
Some examples of how we use the printer: to make cases and stands for the protection of the robot’s electronics; spacers and bearings, camera stabilizers, etc.
Within our team, only four people are allowed to work on the machine, as they have been through the mandatory training, which is offered by the seller.
Students that lack proper training can still model their objects, and their mentors can print the solid piece for them.
Details of our 3D printers:
The printers are 19 cm tall, with a 20x20cm printing bed. The printer’s creations can be printed through SD cards and USB cables.
A matéria prima escolhida para a produção dos nosso objetos é o PLA (plástico de poliácido láctico), um termoplástico biodegradável derivado de fontes renováveis como raízes de mandioca, cana e de amido de milho, por isso a nossa opção, mais ecologicamente amigável.
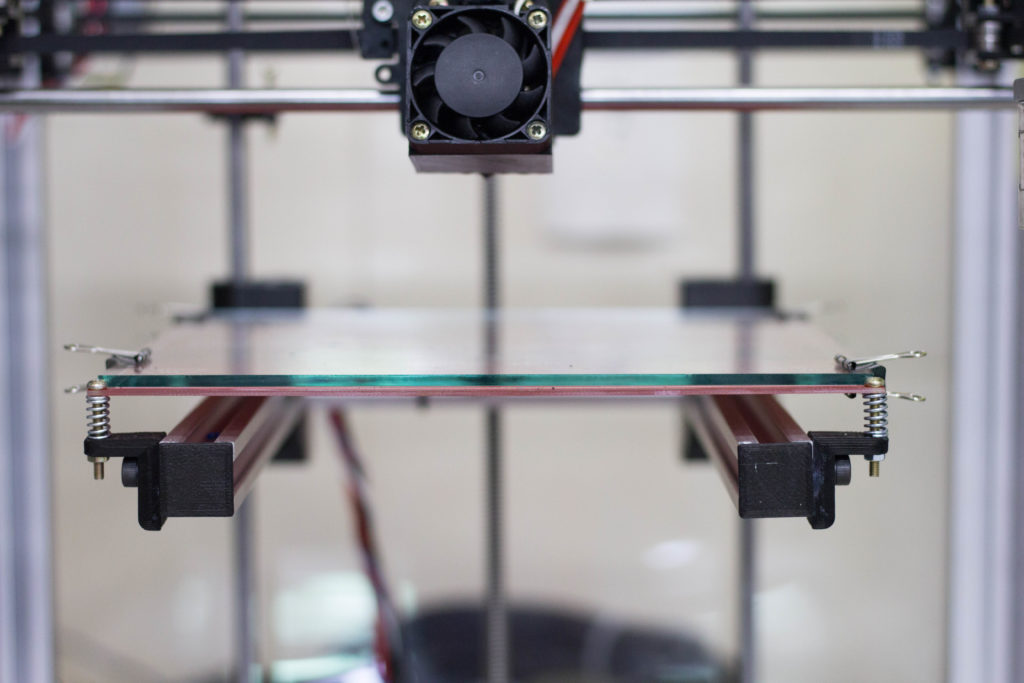
As impressoras têm sido de grande importância durante a nossa Build Season. Com elas conseguimos fazer espaçador, suporte para controlador de motor, engrenagem, chaveiro da equipe, etc.
Comment down below what objects would you print, if you could have one of these printers at home!